Die casting has become an integral part of Malaysia’s industrial sector, supporting major industries, including automotive, electronics, and manufacturing of consumer products. The process of casting metal involves the injection of molten metal into a mold under intense pressure. The result is durable and intricately designed components. Malaysia’s manufacturing industry is a strong one, combined with its skilled workforce and advanced technology, has made it possible to position the nation as a major hub of high-end die-cast items. Many multinational companies have set up production facilities in Malaysia in order to benefit from their competitive pricing and well-developed infrastructure. With the demand in the world for high-tech metal components continues to grow, Malaysia’s die casting industry will continue to grow.
The technological advancements played a crucial role in the growth of Malaysia’s die casting industry. A lot of manufacturers are using computer-aided design (CAD) as well as computer-aided manufacturing (CAM) techniques to boost accuracy and efficiency. Robotics and automation are becoming increasingly used to increase manufacturing speed and minimize the chance of errors. This results in better quality, consistent quality products. Additionally, businesses are exploring green practices like maximizing the use of energy and recycling materials that reduce the environmental impact. These improvements have helped make Malaysian die casting companies more competitive in the global market and attracted customers from all industries looking for precision-engineered parts.
The automobile industry is one major drivers for die-casting in Malaysia manufacturing companies relying on lightweight aluminum and zinc parts to increase the efficiency of their engines and cut emission levels. Die-cast parts such as motor blocks as well as transmission housings and structural elements are essential to modern automobiles, specifically as the demand for electric vehicles (EVs) continue to grow. Manufacturers of electric vehicles require light, high-strength materials to enhance battery efficiency and overall vehicle performance. This has created new possibilities for Malaysian companies that die cast. By investing in the research and development process the companies are staying on top of the latest trends in their industry and addressing the ever-changing demands of the automotive sector.
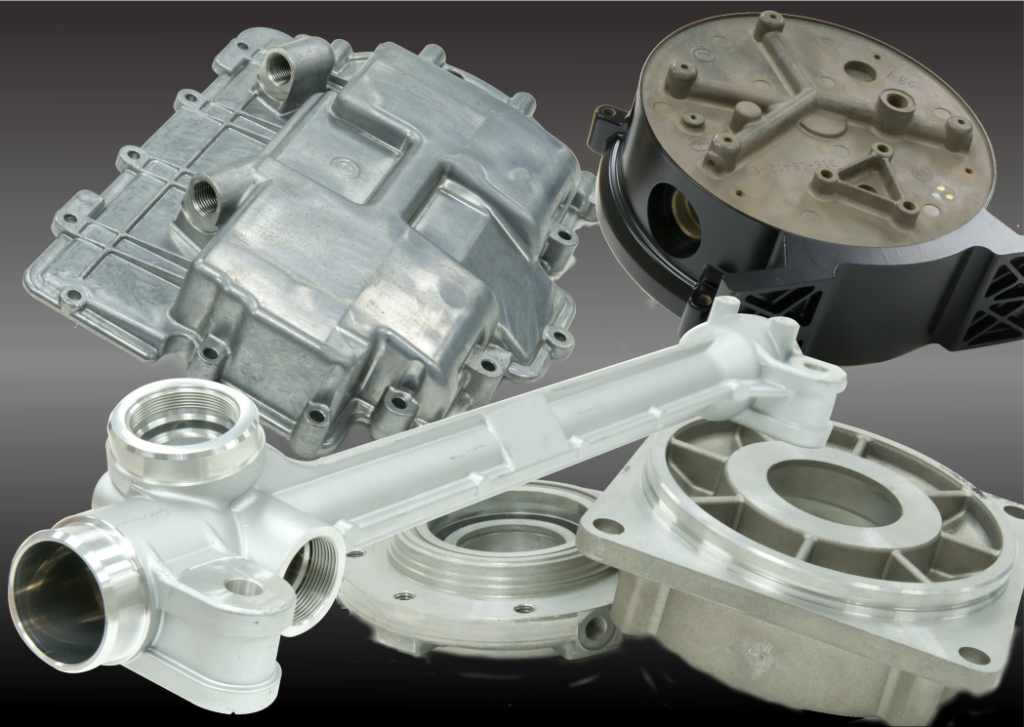
In addition to the auto industry, Zinc plating Malaysia sector plays a crucial contribution to the electronic and consumer goods industries. Electronics industry relies on die-cast parts that are precision designed for gadgets like laptops, smartphones, as well as household appliances. These products require lightweight and durable components that are able to withstand regular use while maintaining a sleek and compact design. Malaysia’s enviable position in electronic manufacturing has led to the need for high-quality die-cast components. In the same way, manufacturers of consumer goods make use of die casting to make cooking appliances, power tools and industrial machinery, benefiting by the capability of die casting to produce intricate and long-lasting metallic parts.
Despite its rapid growth even the die-casting industry is in Malaysia has its fair share of difficulties, including rising cost of raw materials and the competition of other hubs for manufacturing. The fluctuations in the prices of various metals such as aluminum, magnesium and zinc can impact production expenses and overall profit. In addition, Malaysia must compete with bigger producers from China, India, and other Southeast Asian countries, which often have lower labor costs as well as larger production capacity. To keep its edge competitive, Malaysian die casting firms should focus on innovation, high-quality assurance and customer support. By developing value-added services such as prototyping and customized production, firms can distinguish from the increasingly competitive market.
Looking ahead, the future of the die casting industry in Malaysia continues to be bright due to advances in technology and a growing need for precision-engineered components. Integration of Industry 4.0 technologies, including artificial intelligence, machine learning as well as the Internet of Things (IoT) will further enhance efficiency and the quality of die casting production. Sustainability is also an important factor, as companies embracing eco-friendly products and energy-efficient processes to align to global standards for environmental sustainability. As Malaysia continues to strengthen its status as a major manufacturing hub within Southeast Asia, its die casting industry will be a key factor in creating the next generation of engineering precision, providing industries around the world with top-quality and innovative solutions.